数控加工中心是由机械设备与数控系统组成的适用于加工复杂零件的高效率自动化机床!数控加工中心是目前世界上产量高、应用广泛的数控机床之一!它的综合加工能力较强,工件一次装夹后能完成较多的加工内容,加工精度较高,就中等加工难度的批量工件,其效率是普通设备的5~10倍,特别是它能完成许多普通设备不能完成的加工,对形状较复杂,精度要求高的单件加工或中小批量多品种生产更为适用。数控加工中心把铣削、镗削、钻削、攻螺纹和切削螺纹等功能集中在一台设备上,使其具有多种工艺手段。
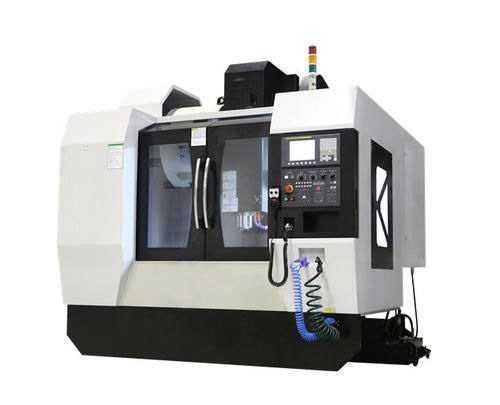
数控龙门高速铣生产商_龙门高速铣价格相关-青岛欧普特精工机床有限公司
(GMSFT等)病确认准确无误之后再启动自动循环,否则可能会造成严重后果!2)还有就是刀补值设定错误。如果刀补值设定错误,也会造成撞刀!要定期检查刀补值是否正确,以避免撞刀事故的发生!数控加工中心导致撞刀的原因很多,但是由系统硬件造成故障的可能性非常小!只要加强管理,减少误操作,定期检查刀补值和工件坐标系的设定,在加工之前确认原点,做好各方面的检查,绝大部分撞刀事故都是可以避免的。撞机现象的产生多是深度Z轴对刀错误以及分中参数错误、刀具选择不合适、手动操作时手轮以及快速进给弄错方向。
2)设定参数有误或者误改动NO000#2INI设定错误0:公制单位1:英制单位。NO3401#0DPI使用小数点的地址字,小数点的含义。省略了小数点时,0:设定*小设定单位1:视为mminch角度为1°。三、加工过程中的误操作1)程序正常加工过程中由于误操作使程序停止下来,如果误操作人员按“RESET”复位之后立即进行循环启动,此时容易发生撞刀。原因:运行的默认值与程序的设定值变化,按:RESET:复位则把CNC系统复位到初始状态,清除了保存在DRAM内的预测程序信息,也有可能改变了刀具的移动指令!
上海五轴数控加工中心
因此操机员一定要注意深度Z轴的对刀位置,底面,顶面,加工面要分别留意!分中的参数要反复的检查,在手动操作时可先把Z轴升高到工件上面再进行移动,要加强机床的操作熟练度!造成曲面精度不够精良的原因多为切削参数不合理,工件曲面表面粗糙、切削刀刃的刃口不够锋利或刀具装夹过长、主轴排屑冲洗功能不良所致.数控加工中心操机人员要不定期检查刀具,对磨损严重的刀具要及时更换.切削参数,公差,余量,转速进给方面设置要合理;在装夹刀具时尽量夹短,刀刃避免太长。
其次是工件坐标系的设定,在进行加工操作前,工件坐标系(G54-G59)的零点设定不正确或者坐标系不正确,此时加工容易导致撞刀或者加工工件的尺寸不正确!二、参数设定错误或者误被改动,在加工时数据单位混乱,工件容易出现尺寸不对或者造成的撞刀1)大家都知道,机床是按照程序走的,如果给定的程序本身有问题,那肯定会撞刀的。FANUC的部分G代码是模态的,如果程序的前一个加工程序或者程序段中制定的G代码在程序段结束时不取消,在下一个程序或者程序段中将继续有效,这样可能致使机床误动作或导致撞刀!
公司拥有先进的技术开发中心和专用检具量具,雷尼绍XL30激光检测仪球杆仪,为数控设备的生产和检测提供强有力的支撑.数控加工中心常见撞刀原因一、机床原点和坐标系的问题会引起撞刀首先我们应该想到的是机床坐标系原点的设定,这个在增量配置的机床*明显,在开机时,机床原点没有设定,这个时候运行程序,不小心就会导致机床撞刀,因为系统不知道机床的确切位置,还有就是机械原点不正确。使用增量位置编码器的机床,回零装快位置不对导致每次回零位置不对,因此需要调整装快位置,若果机械原点设定不正确,运行程序时容易发生撞刀。
普通加工中心,分辨率为1μm,进给速度15~25m/min,定位精度l0μm左右。高精度加工中心、分辨率为0.1μm,进给速度为15~100m/min,定位精度为2μm左右!介于2~l0μm之间的,以±5μm较多,可称精密级.G90指令:按照指令的坐标值运行.G91增量值指令,按照指令的移动距离执行!避免方法:如果自动运行程序过程中出现误操作导致程序停止运行,此时修改为编辑方式,按RESET复位程序,重新运行程序,即使从MDI转换为MEM,一定要检查各个模态代码!
山东明美数控机械有限公司正规有实力,产品质量比较好,型号也比较齐全,我公司和他们合作了很长时间了,你可以了解一下
山东明美数控拥有多年行业经验,质量能保证 ,价格优惠 ,公司正规,实力雄厚,值得去了解下的